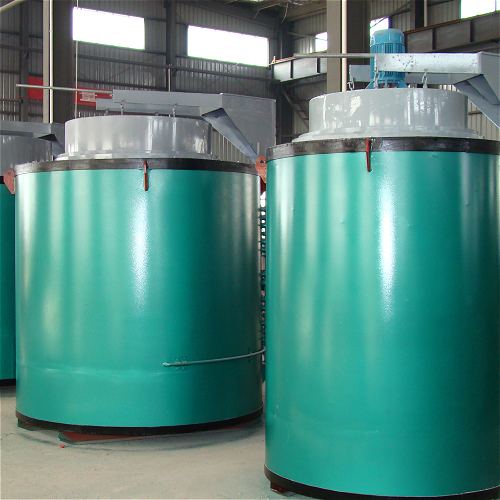
Carbonitriding furnace
- Overview
- Parameter
- Inquiry
- Related Products
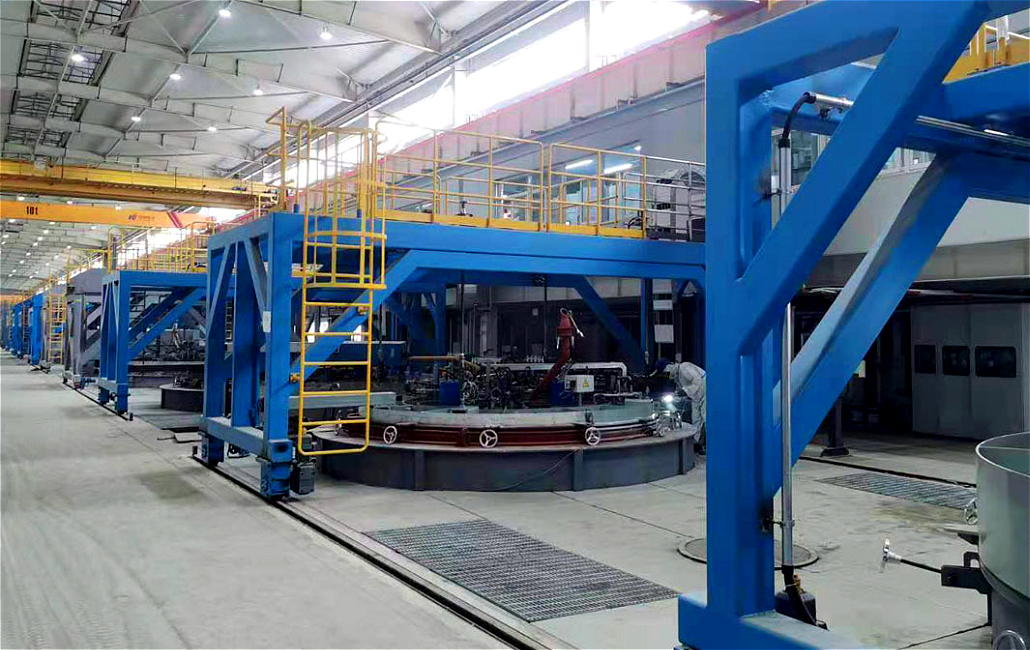
Carbonitriding is usually done at lower temperatures, typically between 850-900°C, while carburizing is usually done at 900-950°C. The lower temperatures help reduce workpiece deformation and grain growth.
The depth of carbonitriding layer is usually between 0.2-0.8mm, which is shallower than the carburized layer. This makes carbonitriding more suitable for workpieces that require a shallower hardened layer.
Carbonitriding can be carried out at a lower temperature, the workpiece is not easy to overheat, and the deformation after quenching is small. In addition, carbonitriding reduces the austenite formation temperature, making the quenching process smoother and further reducing deformation.
Carbonitriding has a faster penetration rate, usually completed within 1-4 hours, while nitriding takes dozens of hours. This greatly shortens the processing time and improves production efficiency.
Carbonitriding significantly improves the hardness and wear resistance of the workpiece surface, while also improving the fatigue strength and fatigue resistance of the workpiece. This is very beneficial for workpieces that require high strength and high wear resistance.
Item | Parameter |
---|---|
Diameter Range | 80mm~600mm |
Pipe Length | 1-10m |
Material | Silicone cloth / non-woven / canvas |
Fabric Thickness | 0.2-0.3mm |
Fabric Width | 110mm |
Metal Strip Width | 11mm |
Metal Strip Thickness | 0.4-0.5mm |
Motor Power | 2.2KW |
Forming Speed | 1-15 m/min |
Weight | 500KG |
Dimension | 2200 X650 X1200mm |