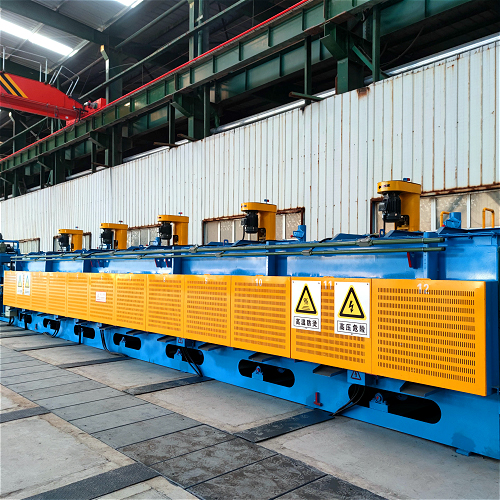
Continuous mesh belt furnace
- Overview
- Parameter
- Inquiry
- Related Products
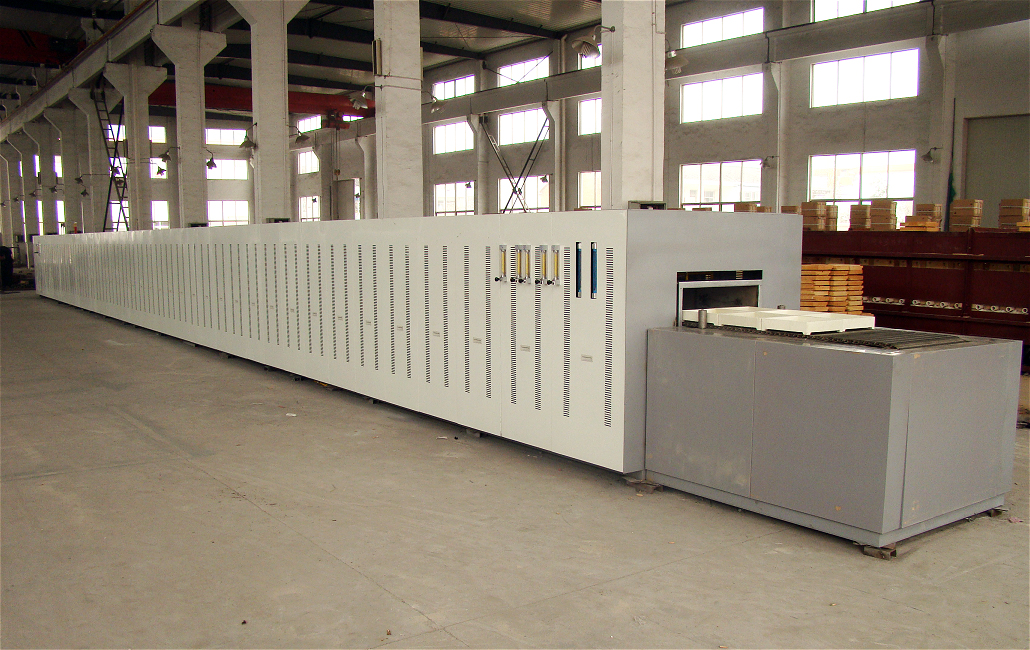
The continuous mesh belt furnace realizes the continuous conveying of workpieces through the mesh belt transmission system, and can perform heat treatment without interruption, which significantly improves production efficiency. This continuous production method is particularly suitable for mass production and can greatly shorten the production cycle.
The mesh belt furnace adopts a closed-loop temperature control system, which realizes automatic temperature control through components such as thermocouples, intelligent PID regulators and thyristors to ensure the stability and uniformity of the temperature in the furnace. Usually, the furnace temperature stability can reach ±1°C and the furnace temperature uniformity is ±10°C.
The mesh belt furnace is equipped with a highly automated control system that can realize automated operations in processes such as loading, conveying, and temperature control. In addition, the equipment also has real-time monitoring and recording functions, and can store a large amount of process parameters and data for subsequent analysis and adjustment.
The use of lightweight and efficient insulation materials effectively reduces energy consumption and reduces the temperature of the working environment. This design not only improves energy efficiency, but also helps improve the working environment
The mesh belt furnace can be equipped with different atmosphere control systems according to specific process requirements, such as a protective atmosphere system, which can achieve bright tempering without oxidation and decarburization. In addition, the mesh belt furnace is also suitable for the sintering of powder metallurgy products, the reduction of metal powders, and the pre-burning and firing of electronic products.
Model |
Medium and High carbon steel perhour (kg) |
Medium and High carbon steel permonth (kg) |
Low carbon steel perhour (kg) |
Low carbon steel permonth (kg) |
Total power |
Medium carbon85% Low carbon70% |
Total length (mm) |
---|---|---|---|---|---|---|---|
CD0-QA | 124-138 | 77-66 | 48-69 | 30-43 | 177-183 | 150/123 | 25495 |
CD0-Q1 | 198-220 | 123-138 | 84-120 | 52-75 | 203-218 | 173/142 | 27995 |
CD0-Q2 | 352 385 | 220-242 | 204-240 | 127-150 | 290-320 | 247/203 | 31495 |
CD0-Q3 | 414-483 | 259-299 | 313-350 | 195 | 353-393 | 300/247 | 31995 |
CD0-Q3A | 506-572 | 316-358 | 413-463 | 218 | 439-464 | 373/307 | 35995 |
CD0-Q4 | 506-572 | 316-358 | 413-463 | 258-289 | 439-464 | 373/307 | 31995 |
CD0-Q5 | 720-780 | 450-486 | 546-598 | 341-373 | 513-543 | 436/359 | 35995 |
CD0-Q6 | 1000-1100 | 624-686 | 833-917 | 520-572 | 615-655 | 522/430 | 39430 |
CD0-Q7A | 1250-1375 | 780-858 | 1040-1146 | 649-715 | 773-828 | 657/541 | 39430 |
CD0-Q7 | 1500-1650 | 926-1030 | 1249-1375 | 779-858 | 928-993 | 788/650 | 39430 |
CD0-Q8 | 1800-1980 | 1123-1236 | 1499-1650 | 935-1030 | 1105-1175 | 939/774 | 43430 |