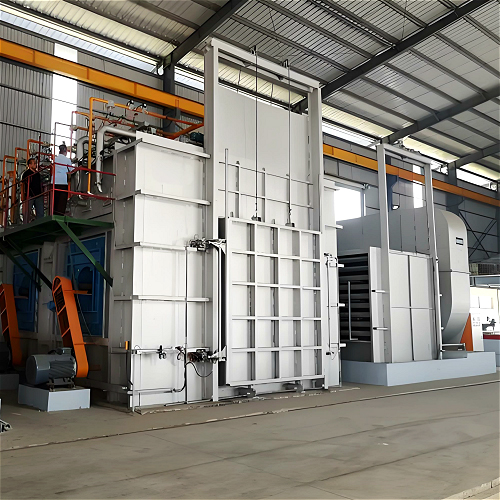
Aluminum alloy homogenizing furnace
- Overview
- Parameter
- Inquiry
- Related Products
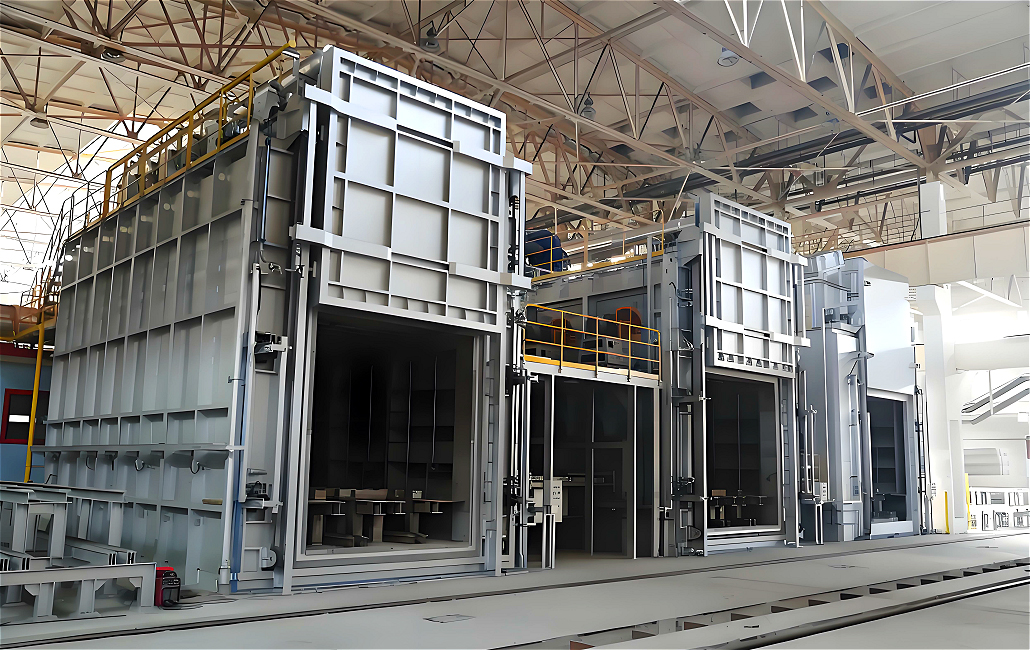
Aluminum alloy homogenizing furnace usually includes heating chamber, cooling chamber and control system etc. Its structural design is to homogenize the internal structure of aluminum alloy material through heating treatment, so as to improve the performance of the material.
By heating, the internal structure of the aluminum alloy material is homogenized, the residual stress generated during the casting process is eliminated, and the metallurgical effect is improved. This process is achieved through an advanced proportional heating temperature control system with a small temperature difference, which can completely eliminate the casting adaptability and component segregation of the aluminum rod, thereby improving the plasticity and strength of the alloy.
It is widely used in the homogenization of aluminum alloy materials, especially in the heat treatment process after aluminum rod casting. It can eliminate the residual stress generated during the casting process and improve the quality and processing performance of aluminum profiles. In the fields of aerospace, automobile manufacturing, etc., aluminum alloys are widely used due to their light weight and high strength. Homogenizing furnaces play an important role in these fields.
High-resistance nickel-chromium alloy is used as the heating element, which has good resistance to high-temperature oxidation and resistance stability, and has a long service life. In addition, its design adopts a high-aluminum ceramic skeleton, which has good high-temperature strength and electrical insulation performance. Reasonable thermal insulation structure design effectively prevents heat loss and is more energy-efficient.
Model | Max Capacity (tons) |
Max Length of Aluminum Rod (mm) |
Max Working Temperature (°C) |
Temperature Uniformity (°C) |
Number of Circulating Fans (sets) |
Fuel |
---|---|---|---|---|---|---|
DM-AHF | 35 | 750 | 610 | ±5 | 3 | Nature Gas |